Project Summary
Built to replace an older sand washing system this plant features the latest washing innovations for washing sand and gravel. Designed for Keohane Readymix in Cork, Ireland, the system features an H30 Feeder, an Aggresand 206, an Aggrescrub 150, an FDU 3000 Floc Dosing Unit and DC 220 Deep Cone Thickener Tank. An as dug natural sand and gravel application is processed into 5 saleable products with 90% of the water being recycled. All of this achieved on a relatively compact footprint, made possible with unique and innovative design choices.
The close working relationship between Keohane Readymix and Terex Washing Systems, along with a high level of aftersales support has resulted in this unique project being commissioned successfully.
Log Washer | Wash Plant | Feeder
| Flocculant Dosing | Deep Cone Thickener
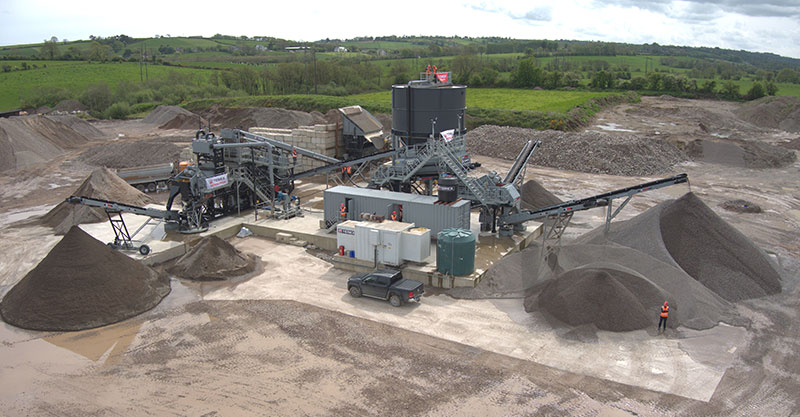
Featured Products
The Latest Washing Innovations
Terex Washing Systems designed, manufactured and installed a full turnkey washing system for Keohane Readymix. Founded in 1979, Keohane Readymix is now serving a broad customer base throughout Ireland with a range of concrete products, sand and aggregates.
The washing solution is situated at their site at Brinny, Co. Cork, which feeds sand and gravel product to other Keohane Readymix sites in the region.
Built to replace an existing wash plant the newly engineered system is capable of up to 150 tph throughput and produces 2 grades of sand and 3 grades of gravel. This is achieved through the integration of several Terex Washing Systems products that have been tailored specifically for this application.
As with any Terex Washing Systems project the first step taken is analysing the feed material. Johnston Patterson, Applications Manager for Terex Washing Systems explained, “The material is a natural sand and gravel deposit which, while fairly free flowing, can get sticky and has some clay through it, as well as some organics, sticks and roots. The feed material is 60/40 sand to gravel and predominantly minus 150mm, but it can be up to 300-400mm. The typical percentage passing 63 micron is around 10%.” The wash plant was designed, using this detailed analysis of the feed material, to meet the finished product specification set out by the customer.
Processing Natural Sand & Gravel
An H30 Feed Hopper was installed at the front end of the washing system with a hydraulic tipping grid that is controlled from the cab of the bucket loader. With the grid at a working angle of 35°, and the spacings on the grid set at 125mm, the H30
Feed Hopper is very effective at removing the oversized and organic material with little overrun of fines. The feeder also contains heavy-duty impact rollers, track rollers and a 4kw hydraulic power pack, which works together to provide a consistent
flow of feed material to the rest of the plant.
A 1 metre wide main conveyor feeds the material to the Aggresand 206 sand cleaning plant. A high capacity wash box soaks the material before it passes on to the screenbox fitted with polyurethane media, which then separates the aggregates into three different sizes while the sand and water is flushed down into a collection sump. Isolated spray bars, a rolling chute and a drop-in platform reduce maintenance downtime and provide easy access to the screen box. Along with the rolling chute the Aggresand range allows users to easily roll the pump out from the chassis so that it can be serviced quickly.
The Aggresand 206 processes the aggregates into four different stockpiles with different grades of sand and stone dewatered and separated into saleable product. The 5-24mm sized material makes its way to the Aggrescrub 150 for further classifying and scrubbing.
The Aggrescrub 150 log washer is packaged on a modular chassis for easy transport and quick assembly. This plant in Cork is pre-wired, pre-plumbed and features a part rinsing sizing screen, a high-volume trash screen and a central collection sump. Neil Rooney, Engineering Manager, explains that, “two rotating bladed shafts introduce energy to the feed stock creating stone on stone attrition, which liberates the conglomerates, and transports them across the water onto the trash screen. Angle adjustment, variable water levels and optional variable speed drives means the Aggrescrub range can cope with the widest feed range”.
Like in any project, the commissioning stage involved a great deal of fine tuning so that this high-performance log washer performed to the standard expected. Gavin Twohig, Operations Manager of Keohane Readymix, said, “we’ve been very happy with the output of the plant. We had decided to put in a log washer system because of the cleanliness of the material. With the log washer on site it’s doing an excellent job and the chips are very clean”.
Water Management System
Any dirty water from the log washer and sand plant is then directed towards the water treatment systems, which are housed and controlled from the Central Control Panel. From here the customer can monitor various elements of the washing system so that
it performs optimally. A popular feature of this control panel is that it allows the Terex Washing Systems service team to dial in remotely to the system and diagnose issues or assist with reconfiguring for new feed material.
The FDU 3000 flocculant dosing unit is housed next to the Central Control Panel and helps to reduce the time needed to recycle water back into the washing system. The 3000 litre, stainless steel tank achieves this by dosing flocculant into clean water that is then added to waste water on its way to the DC 220 Deep Cone Thickener. The flocculant causes particles of silt and clay to bind together, creating a larger mass that then sinks to the bottom of the Deep Cone Thickener while the clean water rises to the top to be re-used. The waste sludge is collected at the bottom of the tank where pressure builds before it is expelled to settling ponds. This process does not require a pump and is executed automatically thanks to the hydrostatic sensor on the side of the deep cone.
This Terex Washing Systems plant takes an as dug natural sand and gravel application and produces high quality natural sand and gravel while recycling 90% of the water.
A complete solution that performs to this level in an aggregate application would not be possible without the close working relationship between Terex Washing Systems and the customer.