Terminology
Rotor
This is the main part of the HSI crusher. It holds the blow bars and rotates at a high speed, being driven by a pulley connected directly to the engine.
Blow bar / Hammers
Wear parts inserted into the rotor which impact the rock to cause breakage. These can be replaced when they are worn down. There are three different options:
- 4 high blow bars
- 3 high blow bars
- 2 high and 2 low blow bars
Aprons
Primary and secondary aprons are used to reduce rock down to the required product size.
Apron Settings
This is the measurement the aprons are set at to achieve the product gradings. Always refer to machine specific operators manual for detail.
Apron Liners
Liners that are generally fitted to the end of aprons to ensure the apron settings can be maintained.
Sometimes called frame liners, these are used on the inside of the impactor body to protect it from wear.
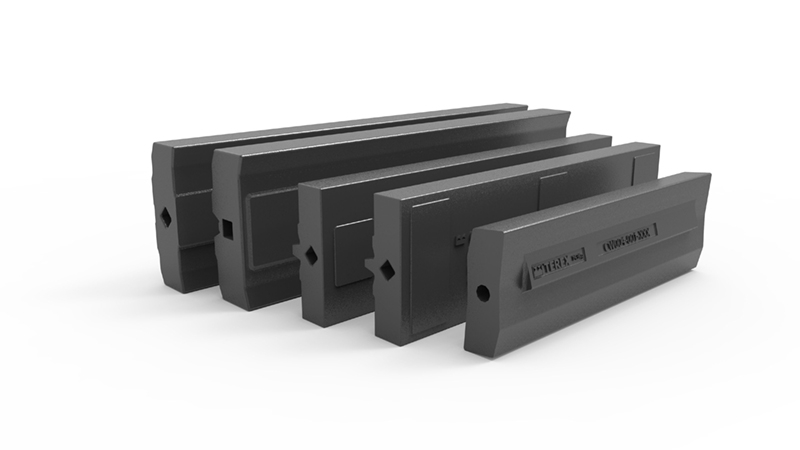
Blow Bar Metallurgy Options
Manganese
Manganese blow bars are typically used in primary crushing applications and will provide the best impact resistance of any blow bar. This alloy is also well suited for applications where tramp iron is possible. This bar will not tolerate abrasive wear nearly as well as some of our other alloys.
Martensitic
Martensitic blow bars are commonly used where the application requires impact resistance and the abrasive wear resist¬ance close to that of chrome irons. Com¬monly used in both primary and recycling applications, this bar will better tolerate larger feed size than chrome iron and will also tolerate moderate amounts of tramp iron. Not recommended for highly abrasive material.
Martensitic Ceramic
Martensitic steel with a ceramic matrix throughout the bar. This bar gives you the benefits of our standard martensitic with the added wear resistance of ceramics inlay. Typically used in primary and recycling applications where a medium abrasive material is being crushed. This alloy would not tolerate very large feed size when compared to standard martensitic or manganese.
Chrome Iron
Chrome iron is widely used in horizontal impact crushers and can provide excellent resistance to abrasive wear in the right application. Feed size and metal content need to be controlled as this type of bar is also more brittle than other alloys and breakage can occur. Typically, this alloy would be used in secondary, tertiary or recycle applications in abrasive material.
Chrome Ceramic
Chrome with a ceramic matrix throughout the bar will provide better wear resistance in highly abrasive material than any other alloy. The chrome ceramic bar would typi¬cally be used in secondary, tertiary and as¬phalt applications where no tramp iron is possible. Ceramics can be combined with either medium or high chrome in order to provide significant wear life improvement over regular chrome bars in the correct application.
Toughened Chrome
Our newest addition to the product range. The toughened chrome bar was designed to offer better resistance to impact over standard high chrome bars whilst still offering a similar abrasion resistance. Concrete rubble with medium iron con¬tent would be the ideal application for this alloy.
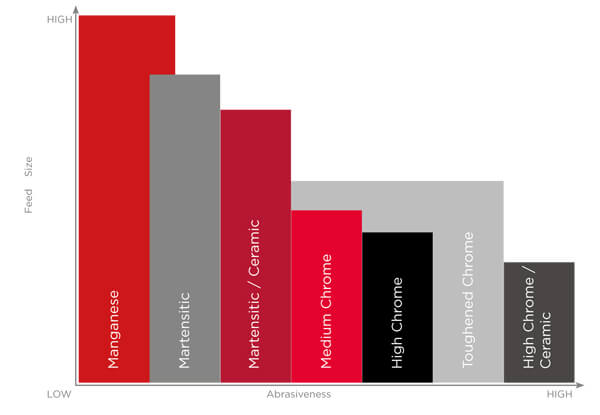
Refer to the chart to help select the proper bar for feed size vs abrasiveness. If you have questions, please contact your dealer to discuss the specific details of your application.
An increase in steel wear resistance (hardness), such as chrome, is normally associated with a reduction in toughness (the impact resistance) of the material.